

Plasma Cutting Tips
Practical Tips You Can Use to Avoid Common Plasma Cutting Problems
Professional welders will still encounter problems when it comes to their plasma cutting problem. These problems may be due to their negligence or it might be that their plasma cutter is not right for them anymore. The welders will always opt for the best plasma cutter as they are the ones that produce the best quality of cut.
The common problems that arise with plasma cutting are oftentimes easy to manage. You simply have to make sure that you find the right resolution to these problems and they are most likely easy to do. Here are some of the simple remedies that one can take advantage of for common plasma cutting problems.
First of all is when you are getting inconsistent or ugly cuts. Consider replacing the consumable parts regularly then. These inconsistent or ugly cuts are produced when the consumables are severely worn which consequently leads to uncontrollable arcing. If you think about it, the performance of a car will not be optimized if you are not replacing the oil regularly. It is the same thing with the plasma cutter. The consumables are the oil. If you do not replace the consumables on a regular basis, then expect the plasma cutter to not have a good performance.
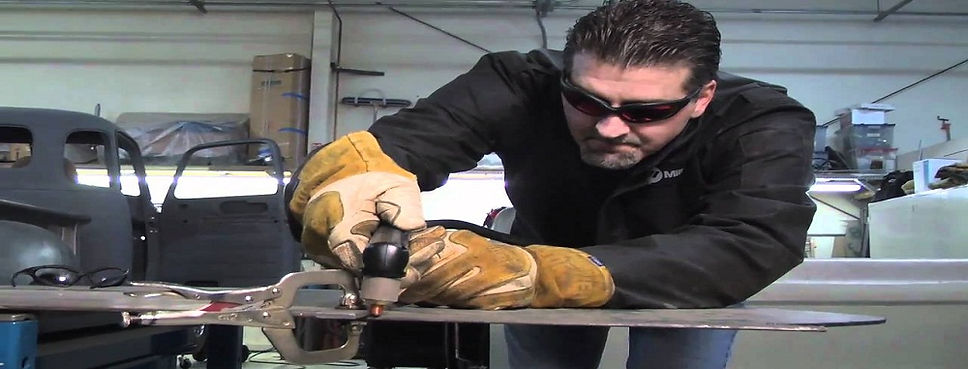
The torch can definitely last a long time. However, that only happens if the torch is assembled properly. You must make sure that the parts are in their right places and they have their proper alignment. They should also fit together snugly. By properly assembling the torch, you can ensure a good enough electrical contact. Moreover, there will be enough gas and coolant flowing through your torch.
Different jobs have different part requirements. It is imperative that you find and use the correct parts for each of your plasma cutting job. The consumable selection should be in accordance to the plasma gas and consumable amperage you are using for your plasma cutting task. The owner's manual should give you an insight on the appropriate matches between the consumable selection and amperage so read through it thoroughly.
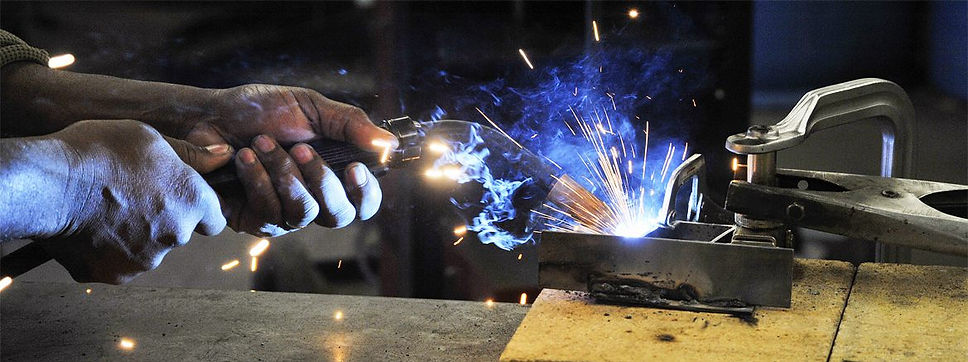
There should be proper flow for gas and coolant. In fact, it is important that you check the flow of gas and coolant right before every use. If there is insufficient flow, then the consumables will not be properly cooled off. The lifespan of these consumable parts will be significantly reduced. If you want to maintain a good cutting arc as well, then you have to ensure that the gas pressure is constant. If there are any in excess, this will just promote hard starting. This is a situation where the torch fails to start an arc despite having all the other normal operating conditions set correctly.
Pay attention to how much O-ring lubricant you are applying. The same with the application of the antispatter compound. Too much of these substances can just contaminate your torch, which consequently leads to premature torch failure. When it comes to the antispatter compound and O-ring lubricant, too much of these substances is never good.